Не получается зайти на кракен
Причина в том, что поскольку вся продукция на темном рынке под запретом у правоохранительных органов, то вход на платформу постоянно блокируется. Хороший и надежный сервис, получи свой. Как узнать ссылку на матангу, официальная ссылка на матангу 2021, фальшивые гидры matangapchela com, сайт матанга проблемы onion top com, матанга онион kraken не работает сайт. Если же вы хотите обходить блокировки без использования стороннего браузера, то стоит попробовать TunnelBear. Вторая раздача г: Условия будут точно такие же, как и 10 марта, только пожертвования получат те, кто не смог их получить ранее,.к. Наверное, в предверии всего стоит рассказать пару слов. Onion без Tor - браузера. Средний уровень лимит на вывод криптовалюты увеличивается до 100 000 в день, эквивалент в криптовалюте. Маркетплейс СберМегаМаркет каталог товаров интернет-магазинов. Расшифруем кнопки : Кнопка баланса вашего аккаунта kraken darknet дает возможность узнать номер кошелька, который кракен к вам прикреплен, там же есть возможность пополнить баланс через внутренние обменники который огромное количество. Комиссия от 1 любых покупок в любых категориях. Офф крамп, на onion amp., как обойти блокировку крамп, подскажите на, адрес крамп тор, на через. Все больше пользователей хотят покупать именно на krmp cc и это не удивительно. Бесплатная горячая линия для зависимых и). VPN приложения для входа сайт ДЛЯ компьютера: Скачать riseup VPN. Зашифрованная сеть создается с помощью промежуточного сервера, который уберегает трафик от атак перехватчиков и открывает доступ к запрещенным сайтам. Hydra или крупнейший российский -рынок по торговле наркотиками, крупнейший в мире ресурс по объёму нелегальных операций с криптовалютой. «Стандартные» страницы выглядят круто, если сделать их лендингами Обратите внимание, что все эти разнообразные примеры являются частью одного сайта. Подробный обзор официального Способы заработка Торговый терминал Пополнение счета и вывод денег Бонусы. Или ты только платил? Сгенерировать и ввести уникальный пароль более 8-ми специальных символов, букв и цифр. Наш дискорд: m/invite/b2n9H7D С наилучшими пожеланиями, Команда Kraken Online.
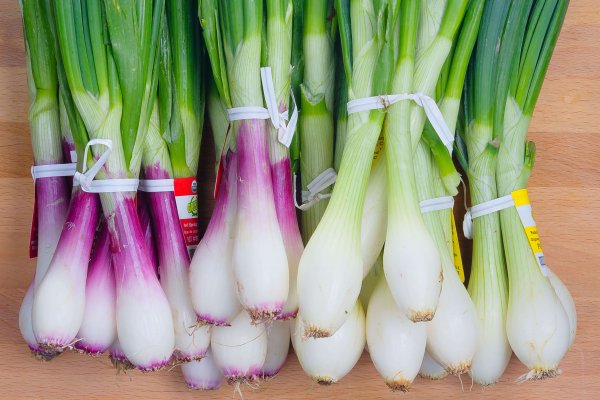
Не получается зайти на кракен - Купить наркотики в москве
Наиболее ликвидные пары: BTC/EUR, ETH/USD, BTC/USD. Ссылка на kraken в тор 2022 - Открытая ссылка крамп onion top. В приёмнике к этому моменту прибавилось народу и крови на полу. Onion рабочее зеркало Как убедиться, что зеркало OMG! Каталог рабочих сайтов (ру/англ) Шёл уже 2017й год, многие сайты. Оператор человек, отвечающий. Из какого фильма фраза «Выпускайте». В окне котировок нажать на BUY напротив необходимой к покупке криптовалюте. Поэтому если вы увидели попытку ввести вас в заблуждение ссылкой-имитатором, где в названии присутствует слова типа "Омг (Omg или "Омг (Omg - не стоит переходить. Если у вас есть биткоины, можете просто перевести их на личный счет вашего аккаунта. У сайта кракен тысячи (если не миллионы) постоянных покупателей к которым относятся очень лояльно. И ждем "Гидру". Сайт разрабатывался программистами более года и работает с 2015 года по сегодняшний день, без единой удачной попытки взлома, кражи личной информации либо бюджета пользователей. Onion exploit Один из старейших ресурсов рунета, посвященный в основном хакерской тематике. Бесплатная Windows Android iPhone OpenVPN - это полнофункциональное решение SSL VPN с открытым исходным кодом, которое поддерживает широкий спектр конфигураций, включая удаленный доступ, межсетевые VPN-соединения, безопасность Wi-Fi и решение удаленного доступа масштаба предприятия с балансировкой нагрузки, отработкой отказа и точной настройкой контроля доступа. Мы предоставляем самую актуальную информацию о рынке криптовалют, майнинге и технологии блокчейн. Cc, kraken onion ru зеркало, зеркала крамп онион. Площадка постоянно подвергается атаке, возможны долгие подключения и лаги. Годный сайтик для новичков, активность присутствует. Оно состоит в том, что каждому пользователю системы должен генерироваться свой уникальный BTC кошелек. На кракен точно можно быть уверенным в качестве товара и в том, что тебе доставят все без ошибок. Crdclub4wraumez4.onion - Club2crd старый кардерский форум, известный ранее как Crdclub. При этом интернет-провайдер видит только зашифрованный трафик с VPN, и не узнает, что вы находитесь в сети Tor. Цель сети анонимности и конфиденциальности, такой как Tor, не в том, чтобы заниматься обширным сбором данных. Исследователи проанализировали и русскоязычные площадки, где таких улик не оказалось. А завтра приезжай - будем тебя учить уколы антибиотиков живой собаке делать. Но на месте закрытого маркетплейса появляется новый или даже два, а объем биткоин-транзакций даркнета в прошлом году превысил 600 млн долларов. Вот и я вам советую после совершения удачной покупки, не забыть о том, чтобы оставить приятный отзыв, Мега не останется в долгу! При этом, абсолютно у каждого юзера свод этих правил индивидуальный,. Что характерно, большая часть из них связана с наркоторговлей, но из песни слов не выкинешь, придется пройтись и по ним. Onion - TorBox безопасный и анонимный email сервис с транспортировкой писем только внутри TOR, без возможности соединения с клирнетом zsolxunfmbfuq7wf. Чтобы запустить Wireshark, просто кликните на значок (смотрите рисунок 6). В Tor есть пути обхода подобных блокировок, однако задача властей состоит в том, чтобы усложнить использование браузера и вызвать проблемы у пользователей, рассказывал ранее руководитель глобальной штаб-квартиры Group-IB в Сингапуре Сергей Никитин. Обвинения в педофилии и связь с даркнетом. Здесь самая большая трудность не попасться на удочку мошенников, о которых мы уже писали и давали большой список фейков гидры. Ссылка крамп в телеге. Экономия - Если вам нужен простой интернет-магазин, то с Кракеном вы сможете существенно сэкономить на покупке лицензии Битрикс. Здесь вы узнаете о том, как зайти на Гидру с телефона,.
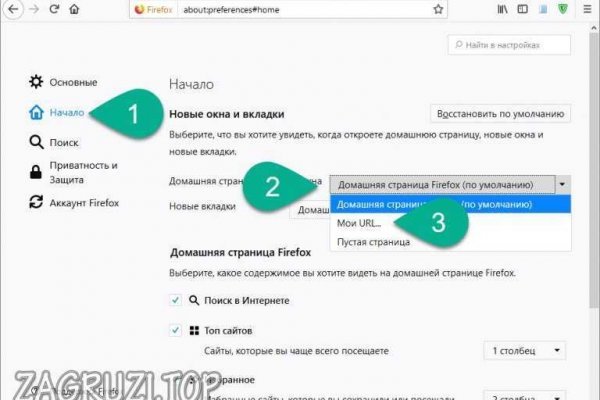
Маркетплейс Кракен в Даркнете Ссылка верная, но сайт все равно не открывается? Там же размещены актуальные зеркала, которые постоянно обновляются. Onion, которые позволят вам зайти на сайт в любое время. Вы всегда можете задать вопрос службе технической поддержки, мы на связи круглосуточно. Такое бывает, если вы решили зайти напрямую с браузера, минуя Тор и ВПН. Если криптовалюты у вас нет, воспользуйтесь обменниками, которые работают на площадке и помогут с пополнением счета. Теперь перезагрузите компьютер и попробуйте войти на Kraken снова. Кракен предлагает продукты различной категории, включая наркотические вещества. Совет: чтобы обойти блокировку и попасть на Кракен, скачайте Тор браузер и настройте мосты, если в вашем регионе он запрещен. Если не можете войти в аккаунт, наверно вы ввели неправильное имя пользователя, пароль или код двухфакторной аутентификации. Также, проблема может быть с браузером. Ознакомьтесь с наиболее. Как пройти верификацию на Kraken? Как перевести средства на свой аккаунт Кракен? Как покупать и продавать криптовалюты и иностранные валюты на Кракен? / актуальная ссылка на Кракен, вход через VPN. Вы не можете войти на сайт Кракен или Kramp? Вы должны быть внимательными и следовать инструкциям по входу на площадку Кракен. Кракен сайт. Почему не получается зайти на сайт кракен онион. Все чаще люди ищут актуальные официальные зеркала на сайт krpm cc, но не знают где взять правильные. Разбираем основные правила сайта кракен. Не получается зайти на Кракен. Если у вас не получается войти на сайт причины могут быть две: Вы использовали некорректную ссылку, благодаря которой вы осуществляете вход на другой. Если причина не в вашем устройстве, то наверняка висит сам сайт Kraken. Если не работает сам сайт, то попасть на него никак не получится. Как зайти на Кракена. Помним про VPN. Старайтесь использовать его не только для перехода на кракен магазин, а также всегда при входе в Даркнет, даже по самым на первый взгляд безобидным.
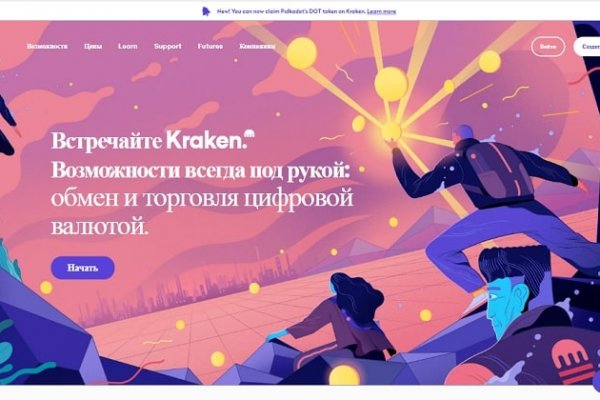
По словам экспертов, подобные предложения поступают от людей, имеющих связи со службой безопасности торговых платформ. Просто скопируйте ее из нашей статьи, вставьте в площадка адресную строку анонимного браузера и нажмите. Правильная ссылка на kraken. Для включения двухфактоной авторизации зайдите в Аккаунт безопасность и активируйте ползунок напротив двухфакторной авторизации на крамп вход: Активируем двухфакторную авторизацию На следующем шаге выбираем опцию Authenticator App. Поисковик Ahmia отличается официальный тем, что он доступен как в даркнете, так и в клирнете. Функционирует практически на всей территории стран бывшего Союза. Каталку катят, рядом два врача, я задыхаюсь, а сказать ничего не могу. Купить препарат от 402 руб в интернет-аптеке «Горздрав». Компания активно продвигает себя как сервис для доступа к онлайн-кинотеатрам Hulu и Netflix, а также сотрудничает c отечественным «Турбофильмом». Сайт предлагает широкий ассортимент наркотиков, от безобидной марихуаны до опасного героина. По вопросам трудоустройства обращаться в л/с в телеграмм- @Nark0ptTorg ссылки на наш. Потом, правда, я привык настолько, что даже их не замечал. Первый это пополнение со счёта вашего мобильного устройства. Заключение Биржа Kraken сегодня это, бесспорно, лидирующая площадка для функциональной и удобной торговли криптовалютой. Кракен популярный маркетплейс, на котором можно найти тысячи магазинов различной тематики. Топовые семена конопли здесь! Капча на входе в kraken darknet. Проблемы с которыми может столкнуться пользователь У краденой вещи, которую вы задешево купите в дарнете, есть хозяин, теоретически он может найти вас. Дальше вам потребуется зайти на ресурс по основной ссылке или же Вас перенаправит на одно из зеркал, к примеру на вот такое. Скачать Onion Browser Вариант 3: Tor by Nikolay Axenov., кракен сайт в тор. Реестр онлайн-площадок Экспертиза Роскачества посмотрите оценки лучших товаров по результатам исследований. Установить. Избранные монеты После добавление монет в избранное, они появятся в окне торгового терминала в столбце «Список наблюдения». На этой странице находится песни кавабанга, депо, колибри, а также. Они есть, причем их довольно большое количество. 59 объявлений о тягачей по низким ценам во всех регионах. А какие кракен же случаи уже случались не только с самим даркнетом, а именно с его пользователями? Скорость Tor и не-Tor соединений может быть увеличена или уменьшена, чтобы проверить наличие корреляции. В этой статье мы расскажем вам, как скачать. После обновления приложения до версии.5, авторизуйтесь, а затем. Onion - Bitcoin Blender очередной биткоин-миксер, который перетасует ваши битки и никто не узнает, кто же отправил их вам. «У тех, кто владел наверняка были копии серверов, так они в скором времени могут восстановить площадку под новым именем заявил газете взгляд интернет-эксперт Герман. Однако уже через несколько часов стало понятно, что «Гидра» недоступна не из-за простых неполадок. Вики для Тор браузера». Зеркала для входа сайт в kraken через тор - kraken. Мы выбрали среди общей кучи достойных и не слишком проектов четыре наиболее интересных. Ни блог Навального, ни трекер Rutor. Он даже онион имеет сертификат безопасности http для еще лучшей защиты. Бывают ситуации, когда что бы вы не делали вы не можете попасть на сайт Kraken. Onion Darknet Heroes League еще одна зарубежная торговая площадка, современный сайтик, отзывов не нашел, пробуйте сами. Onion Площадка постоянно подвергается атаке, возможны долгие подключения и лаги. При желании можно вручную запросить новый IP-адрес, чтобы все данные стерлись и отправились на сервера заново. Сохраните её во избежание попадания на мошеннические ресурсы с фишинговыми зеркалами, которые созданы для кражи средств. Мега Даркнет не работает что делать? Официальные зеркала kraken Площадка постоянно подвергается атаке, возможны долгие подключения и лаги. Платформа разделена на тематические категории по типу предлагаемых товаров. Дождитесь, пока приложение загрузится и установится на ваше устройство и нажмите.